The long value chain of plastics packaging, from manufacturers to converters to brand owners, is turning a wary eye to state-level recycling developments. Those developments include new laws labeled as extended producer responsibility (EPR), but they fall short of serving as models.
However, the industry hopes to bring about a workable national policy that brings consistency, a steady and inclusive supply of materials, and innovative infrastructure to recycling. Paving the way there, industry leaders are collaborating on solutions that set an example and create clear, constructive pathways for the industry—and policymakers—to follow.
EPR started as a solution to recycling hard-to-handle products, such as electronics and household hazardous waste. As it evolved to include producer responsibility for packaging, the concept ran aground against China’s rejection of materials for recycling in 2018.
“We can’t just continue to put our recyclable materials or our waste on containers and expect that they’re going to end up in China to be recycled,” says Andy Hackman, a principal lobbyist at Serlin Haley in Washington, D.C., and lobbyist for the Flexible Packaging Association (FPA). “Finding the new future of recycling is what this debate is all about. In particular, it’s focused on having producers, in essence, pay for or recycle or reuse their items, or creating incentives to recycle.”
New Laws
In 2021, Maine and Oregon became the first two states to adopt laws styled as EPR solutions, with six states queuing up to consider the issue in 2022, Hackman says.
In the view of the industry, neither law fits the definition of EPR. In Maine, municipalities have frontline responsibility for recycling, and the state Department of Environmental Protection sets policy directions. “Other than paying a check to the stewardship program that is selected by the department through an RFP (request for proposal) process, that’s really the only input producers have,” Hackman adds.
In Oregon, an advisory council that includes several producer sectors—brands, plastic, paper—has input into decisions made by the state Department of Environmental Quality (DEQ) and a Producer Responsibility Organization (PRO) established to operate the system.
“There are a lot of checks and balances within the Oregon system giving the industry more comments and questions to what the DEQ is deciding, not necessarily just through the PRO but through that council,” says Lauren Aguilar, government affairs associate for Serlin Haley, also lobbying on behalf of FPA.
Workable EPR programs must “provide more value and benefit than the cost and complexity they introduce,” says Elizabeth Rhue, staff vice president of global sustainability at Sonoco, based in Hartsville, South Carolina. “Any program that is introduced has to be effective and efficient and not overly burdensome to the industry.”
Programs should be fair across packaging platforms and promote inclusivity, Rhue says. The industry should “push back against any EPR programs that attempt to limit what should be recycled.”
Current recycling systems need improvements, but only EPRs that are well-crafted offer a solution, says Phil Rozenski, vice president of public affairs for Novolex, also based in Hartsville. An effective system requires sustainable finances to guard against the ups and downs of government funding, coordination that allows for future growth, and helps to target needs as they arise, as well as having more infrastructure than the Maine and Oregon laws create.
“After 2022, the gate is going to fly open, and these issues will be popping up in a lot of states.”
—Lauren Aguilar, Serlin Haley, and FPA Lobbyist
“Infrastructure isn’t just collection and processing materials into bails,” Rozenski says. “Infrastructure also includes—and most importantly includes—reprocessing it into usable materials and reusing it in new packaging and products.”
After all, he says, the current problem came not from a lack of collection capabilities, but the sudden disappearance of reprocessing capabilities when China closed its doors.
If shaped within the parameters of an American-designed producer responsibility system and used as a model for infusing uniformity into localized recycling systems, the resulting approach would allow “innovation and competition and community engagement to continue to flourish,” he adds.
“This helps build basic collection and access and outreach infrastructure, but it doesn’t create monopolies and doesn’t end up as a takeover of the waste system,” Cookson says. “The money doesn’t go to the government. It’s about creating that supply.”
Achieving Circularity
The challenge with the laws of Maine and Oregon is their support for existing, entrenched recycling systems. Maine’s law offers little ability “for the makers of flexible packaging or the brands that use flexible packaging to help pull those materials back from going to the landfill,” Hackman says. “There’s a focus on supporting the recycling we know today.”
Oregon offers some avenues toward new infrastructure and bringing materials into greater circularity, but with the DEQ as gatekeeper it lacks the kind of control that producers need for direct involvement in the solid waste system, Hackman says.
Manufacturers “absolutely” have a responsibility to continue striving for circularity, Rozenski says. “EPR should fund the missing pieces of circularity,” he says. In a product’s life cycle, packagers might sit on a certain segment of the circle, while EPR “helps build the
rest of that circle so it can come back to us. We need to work toward ways to make things that can fit in a system that brings them back and uses them again as much as we can.”
Including advanced recycling in circularity plans is a key step toward equity in recycling, Cookson says. By returning plastics to their basic chemical components, advanced recycling can generate virgin-equivalent packaging safe for sensitive uses. The advanced recycling landscape is attracting a growing list of high-powered investors, including ExxonMobil, Shell Chemicals, Chevron Phillips Chemical, and Eastman Chemical Co. With $4.3 billion in investments since 2017, companies are exploring “different types of technologies that take different feedstocks and produce different products.”
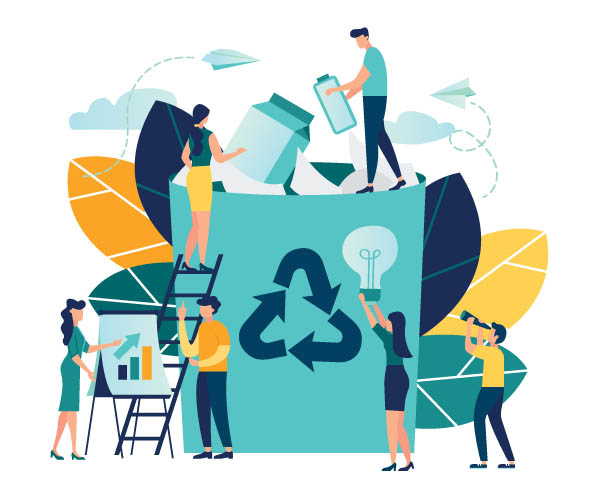
“We want to make sure that advanced recycling counts toward circularity, because it’s a little bit different than mechanical recycling, especially as there will be challenges in getting mechanically recycled content into food and pharmaceutical and medical contact packaging,” he says. “You’ll definitely need advanced recycling to reach that goal.”
Cookson sees a “real hunger” for bipartisanship on recycling, but Congress still needs education, including details on the power and potential of advanced recycling. The U.S. Environmental Protection Agency (EPA) and the Department of Energy (DOE) are also “taking a lot of steps in the right direction,” although the EPA’s proposed national strategy doesn’t include advanced recycling—an oversight that Cookson hopes will be corrected in the final draft.
Raising the Industry Voice
Meanwhile, legislation to reform recycling in an EPR-like fashion could see movement in 2022 in Connecticut, Washington, New York, Vermont, California, and Maryland.
So far, Maryland’s efforts have come closest to a model, Hackman says. In all states, producers need to participate early in legislative processes to assure that the final bills approach circularity.
“It’s critical that we get something on the books that looks more consistent and more constructive to get producers involved in the system,” Hackman says. “The industry must offer a clear vision for what we think is more workable and get it passed in one or two states.”
Staying active in industry associations builds a company’s voice, Aguilar advises, and so does building personal relationships with state legislators and members of Congress, “because you have somebody who’s fighting for you and somebody who understands your issues.”
“After 2022, the gate is going to fly open, and these issues will be popping up in a lot of states,” she says.
“Opening up the doors to relationships now will be key in getting the discussion going in a positive light, so they understand our side in how it works. They’re not getting just one side of the story.”
In its advocacy, Novolex points to the FPA/Product Stewardship Institute agreement on the eight key elements of EPR as a guide to well-crafted legislation. All companies “have to be engaged,” Rozenski says. A key flaw in Maine’s bill—designating the PRO through RFP, which takes industry out of the process—heightens the imperative of industry involvement as EPR policies roll out state by state.
“I cannot stress enough that we need to support FPA so we have a voice in this,” Rozenski says. “Money will be collected and spent on infrastructure, and we need to be represented.”
A Patchwork System
Hackman points out that recycling is a service that is provided locally.
Although packagers are experienced at working across jurisdictions, a jumble of state recycling systems, each pursuing its own idea of EPR, could create compliance nightmares. If the PROs created to implement programs are not structured to incorporate industry voices, “it’s going to make it extremely challenging for the ability of the producers to uniformly sell products and assure they are in compliance,” Hackman says. “It will take a lot of staff work to pay the appropriate fees in the different states and organizations that are supposed to ensure compliance on their behalf. If you have something like a separate organization for each state, it’s going to challenge the ability of interstate commerce to flow.”
The packaging industry’s best hope is a strong effort “for collaboration on a national structure that will ensure compliance in each one of these states,” Hackman says. There would still be differences, but a strong national PRO structure could “feed out into the states in a way that is, at least, as consistent as possible.”
Sonoco relies on team members with expertise in a range of areas—technical packaging, legal, operations, life cycle—to analyze the regulatory and legislative information supplied by partners in associations and government relations firms, Rhue says. Those analysts create actionable information so Sonoco and its sustainability division know “how it directly affects us and where we need to move and where we need to monitor.”
One of the lenses the analytics team brings is understanding how emerging regulatory and legislative activity impacts customers who have made their own public commitments to sustainability.
“It’s a responsibility we have to our customers, helping to be a partner and developing solutions with them and otherwise ensuring compliance with any existing solutions we have off the shelf,” Rhue says. “We see ourselves as playing a role in being a go-to and an expert for our customers.”
Elevating Sustainability
Packagers make different claims based on the sustainability benefits of their products—lightweight, fewer greenhouse gas emissions, more recycled content, easier to recycle, better at preserving products. While flexible packaging producers and converters seek inclusion in EPR programs, they must perform a “balancing act” around how producers are making decisions and how brand owners want their products to be perceived, Hackman says.
“It’s going to take more engagement in the solid waste sector in terms of sustained investment in helping manage this material to deliver on stated goals but also in terms of public perception,” he adds.
Education on the full spectrum of plastics’ benefits is crucial, Aguilar says. “I don’t think that everyone understands the entirety of the environmental impact of these materials,” she says. “There’s a reason behind the use of lightweight materials, but not everybody thinks that far.”
Wide-ranging industry consortiums and associations that develop guidelines around packaging design help players keep pace with—or even get ahead of—a changing sustainability environment, Rhue says. “It has to be an effort across the entire value chain, from raw material suppliers to converters to brand owners and a host of other partnerships and training groups working along the way,” she says. “We have to make sure that we are driving alignment within the industry on the things that are most critical and important to the industry as a whole.”
Sonoco has memorialized its broad sustainability goals by driving down into each of its businesses with “specific, robust, and comprehensive road maps” to help them understand how they reach those goals.
“We’re incorporating not just technology but thinking about our entire value chain,” Rhue says. She asks: “What do suppliers bring to the table? Where do we need to engage our customers? How do we communicate the progress and the pitfalls and go back to being collaborative? Is there information we can share and learn from others that helps in delivering those goals?”
M. Diane McCormick is a freelance writer and editor based in Harrisburg, Pennsylvania.