Lantech doesn’t make flexible film or film alternatives. However, the international manufacturer of packaging machines has an interest in closely monitoring the evolving marketplace and efforts that might limit the use of virgin plastics.
Founded in 1972, Louisville, Kentucky-based Lantech makes machines that allow other companies to prepare their products for shipment, including automatic and semi-automatic stretch wrappers that stabilize and protect large loads. So, its leaders set out to study several alternatives to virgin resin and how well they hold up to stress tests that simulate pallets in transit. In a report first released in October 2022, the company found that virgin resins outperform alternatives on the market, including stretch films using 30% post-consumer resins (PCR) and paper options.
The report titled “Stretch Film Alternatives: Evaluating Performance and Environmental Impacts” was updated in the fall of 2023 to include a higher-quality PCR product new to the market.
“In the beginning, our research was primarily to serve the growing needs of our customers,” says Grace Lancaster, Lantech product manager. (The company’s white paper can be found at lantech.com/film-alternatives-project/.) “The most relevant sustainability information Lantech can provide is testing data on optimized machines. We rigorously tested each alternative, and these are the results: a real, no-greenwashing approach. What we show is realistic and applicable for manufacturing environments.”
The Journey
Research and development (R&D) has been a part of the company’s DNA going back to when Lantech was founded by her grandfather, Pat Lancaster, and his brother, Bill, in 1972. Lantech patented the first machine of its type that could automatically wrap pallets of boxes, a system that has been copied by numerous other companies since then, Grace Lancaster says.
A few years ago, when an international consumer packaged goods (CPG) company asked about switching from resin plastic wraps to paper, Lantech investigated. As more companies began making similar requests, Lantech officials wanted to ensure its customers were making informed decisions, so the research intensified, leading to the white paper in 2022.
“This is a direct response to customers who have asked us about running film alternatives,” Grace Lancaster says.
Pat Lancaster, who has developed hundreds of patents since he co-founded the company, determined early on that a lot of claims about alternatives to resin were false or that the options weren’t being evaluated with proper containment force standards, Grace Lancaster says.
The company’s goal evolved, accordingly. “While we need to address the needs of our customers, we must also address the broader narrative,” she adds.
While the results of the tests show that virgin material is superior in cost, carbon footprint, and performance to alternatives, she stresses that the company will support customers to use any stretch film alternative that meets their needs and mandates. Some customers might have reasons for wanting to use paper, she explains. “That is their decision, and we are just here to help.”
Once a decision is made, Lantech can tune machines that use flexible films to optimize performance for variations among virgin films. Machine recalibration is involved if a company decides to go from virgin material to 30% PCR. If switching from flexible to paper, the materials are fundamentally different, so the changes are more complex, requiring a retrofit of a machine’s hardware, Grace Lancaster says. “The key is to optimize the machine based on the material you are using,” she adds.
The Testing
The company’s tests focused on a 100% virgin material, a standard-grade 30% PCR, an ultra-grade 30% PCR, a perforated paper, and a kraft paper material.
It then had its machines automatically wrap a pallet of boxes with each material. The pallets were put under an EUMOS standard acceleration test that moved the pallets along a sled as if a truck was going from a stop to a start. The pallets were then moved to a platform that vigorously shakes the pallet—an orbital shaker table—to simulate the jostling that would happen during shipment.
All the materials passed the tests.
However, the research determined that the 100% virgin film had the lowest cost per load at 54 cents per load. It was followed by the 30% PCR ultra film at 69 cents. The 30% PCR standard-grade film registered at $1.10 per load, while the kraft paper came in at $2.70. Perforated paper was the highest at $7.77 per load, according to the updated report released in the fall of 2023.
The weight per load and carbon footprint results were:
- Virgin film: .29 pounds per load, with .33kg of carbon dioxide (CO2)
- 30% ultra-grade PCR: .37 pounds, with .38kg of CO2
- 30% standard-grade PCR: .60 pounds, with .61 kg of CO2
- Kraft paper: 2.12 pounds, with .46 kg of CO2
- Perforated paper: 4.73 pounds, with 1.02 kg of CO2
Although paper works, its performance is much lower, Grace Lancaster says. Paper is not stretchable like ordinary film and does not conform to the load shape.
“We address paper, but we wanted to get into the weeds on the PCR argument,” she says. “That is where it gets tricky, and that is where everyone wants to know what is going on.”
Standard-grade 30% PCR can be problematic because the recycling process leaves gels that can become holes, which can cause film breaks, lowering overall performance. Many different suppliers provide 30% PCR, all of similar quality results, Grace Lancaster says.
The original tests in 2022 didn’t include an ultra-grade 30% PCR. Lantech agreed to include one sample of the ultra-grade PCR in its 2023 addendum because the sample has been newly introduced into the market. While it performed much better than standard-grade PCR, she cautions that the sample’s production was tightly controlled.
“It’s not scalable right now for the volume of production we see at our major customer sites, but we give it the benefit of the doubt to showcase the potential of PCR when supply is steady,” Grace Lancaster says. She would like to see further testing that includes multiple samples of the ultra-grade PCR where there might be variances and to show how the performance might be sustained over time.
Grace Lancaster says she is confident that the R&D being conducted by numerous stakeholders into PCR will continue to show improvements.
Supply, Demand, and Regulations
One concern among industry stakeholders is that the demand for PCR has been outweighing supply. “Today, that is true, but it is changing quickly,” Grace Lancaster says. “We are seeing millions of dollars flowing into infrastructure, so we are on the precipice of that changing.”
Meanwhile, government regulations increasingly require PCR mandates, especially in Europe where laws have been in place for years. In the U.S., four states have passed extended producer responsibility laws—California, Colorado, Maine, and Oregon—and they still are working out the details of their programs.
Lantech steers away from advocacy or getting directly involved with legislators. The company has spread the word about its findings through its suppliers, distributors, and vendors, as well as industry shows such as PACK EXPO Las Vegas held in September. Other stakeholders have started using Lantech’s findings in their advocacy efforts, Grace Lancaster says.
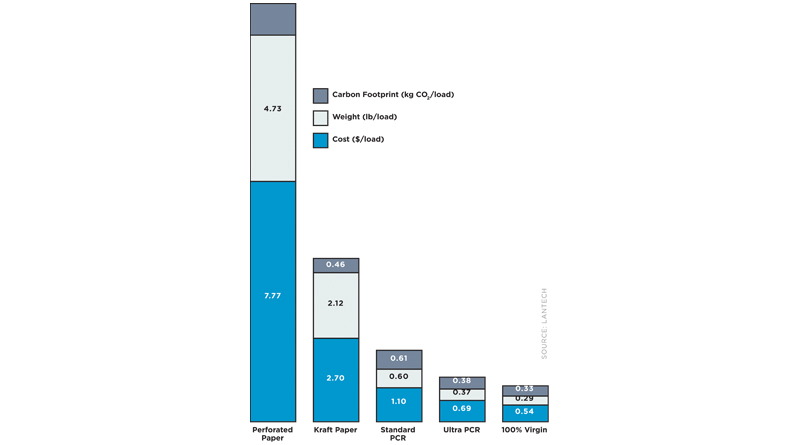
Lantech’s findings aren’t unique, she adds. Others have done similar tests and made similar conclusions, including the Stretch Wrap Alternative Project (SWAP) started by Microsoft.
Microsoft is direct about its intentions. It wants to eliminate the use of single-use plastics from its packaging by 2025. In the SWAP report, the company points out that it cannot resolve the complex issues on its own, so its research has been supported by 10 additional companies from the Ellen MacArthur Foundation network, including BASF, Cisco, the Estée Lauder Companies Inc., and FPA member Berry Global Inc., according to the SWAP website.
The 2022 SWAP report points out that “stretch wrap is the industry standard for securing pallet loads because of its performance, flexibility, and favorable economics. It can be applied to nearly any load shape, colored to hide products, is inexpensive, and allows easy handling. It’s a challenge to find comparable alternatives.”
The report also gives a nod to how flexible films contribute less to greenhouse gas emissions than alternatives.
Lantech recognizes that policymakers are concerned about the environmental impacts of stretch film and directly addresses the matter in its white paper. “Lantech and its customers are part of the overall impact that manufacturing and shipping goods have on our planet,” the company says. “… Working together for better outcomes, the packaging industry has the power to substantially reduce waste in the global commerce system.”
Stretch film used to increasingly wrap pallets and packages is considered a single-use plastic in various legislation, the report also notes. “Pressure on elimination of single-use plastics places plastic stretch films under increased scrutiny by governments and corporations,” the report says. “In 2019, nearly 2.4 billion pounds of polyethylene resin was consumed in the production of stretch film.”
Recognizing the concerns but knowing that flexible films also outperform alternatives, Lantech makes several recommendations in its report that might help reduce the amount of film needed. For example, loads could be wrapped more efficiently so less film is used. Proper machine calibration and machine maintenance would help, as well.
“The potential to reduce film without the need for substitutes or replacements is a major opportunity for manufacturing and distribution centers,” the report says. “… Improvements in wrapper technology and film quality could also contribute to reduced weights to achieve required containment.”
Future Research
Lantech intends to continue its research as new films and alternatives are introduced. Future updates might be a new white paper or another addendum to the original report. “It’s ongoing. There is new stuff coming out all the time. There are bioplastics films that we are going to test and start to talk about,” Grace Lancaster says. “Our customers continually ask us about new developments.”
And the decisions will remain with the customer. “We are being objective,” she says. “But at the end of the day, we want our customers to know that virgin material—according to this research—is a remarkably efficient material when compared against cost and carbon footprint. These are simply Lantech’s test results. Hopefully, they can help inform decisions and inspire others to conduct complimentary research projects.”
Thomas A. Barstow is senior editor of FlexPack VOICE®.