After an FPA Emerging Leadership Council (ELC) committee on recruitment was formed last year, its members quickly determined that they would need to branch out beyond traditional internship programs.
The top packaging schools nationwide, including Clemson University in South Carolina and the University of Wisconsin-Stout, place students in expansive internships that attract top talent interested in packaging engineering, sales, marketing, and other experiences that will further their careers. Yet worker shortages that are hindering industries nationwide—from manufacturing to construction to health care—demonstrate a dire need for people with trade and technical skills to run the modern machinery and plants that produce flexible packaging.
“Every single company has to articulate on the front end how in some way, shape, or form that they are, in fact, in the business of environmentalism.”
—Richard Barnhouse, president, Waukesha County Technical College, Wisconsin
“One of our first missions as far as the recruitment strategy was to listen to some of the gaps and challenges with recruiting and retaining talent. We have a multifaceted approach,” says Apurva Shah, who is chairperson of the committee. But the interviews highlighted something: “We need to work with vocational schools to fill key technical and skilled jobs.”
One example is flexographic printing, explains Shah, who is senior marketing manager at Charter Next Generation. “It’s an art. It’s a trade,” he says, adding that skilled workers continually retire without replacements coming behind them. “There are people skilled in that field that we are losing day by day.”
One long-term goal of the committee will be to rekindle relationships with vocational schools that either don’t have a program to promote technical skills in packaging or schools that the FPA has lost contact with over the years. The committee would then develop resources that FPA members could use to find workers in their towns and cities.
“That is an example of one initiative,” Shah says about the work of the committee, which is one of four under the ELC. (The others are education, leadership development, and advocacy.) Several other initiatives from the recruitment committee will roll out over the next three years, including the ELC committee’s first program that launched this summer. It involved creating a network of interns across FPA member companies who could meet with peers and mentors to learn about the industry. In future years, the committee intends to create a resource where FPA member companies can recruit students through live networking events.
Researching Schools
The strategy with vocational-technical and trade schools is still in its infancy but was hit upon by listening to the concerns of hiring managers. Shah says the effort is being led by Mathieu Jeanneau, a committee member and vice president/COO of St. Johns Packaging Ltd. A detailed plan will take time to develop, partly because vocational training is hyper-local, with schools catering to the specific needs of industries in their areas. The idea would be to identify up to about 10 schools that have robust programs, learn from what they offer, and then develop actional ideas for FPA members. The vision is that schools could develop programs that better fit the needs of the flexible packaging industry, Shah says.
One school that came up in the discussions was Waukesha County Technical College (WCTC) in Pewaukee, Wisconsin, Shah says. WCTC is part of the Wisconsin Technical College System, a network of 16 technical schools statewide that work with local companies and chambers of commerce to develop skilled workforces for their communities. In Wisconsin alone, FPA has over 35 members who either have a headquarters and/or plant in the state, says Dani Diehlmann, FPA vice president, communications.
Speaking generally, WCTC President Richard Barnhouse says it is not unusual for a company to approach the school about a problem and for a curriculum to be built around solving it. WCTC has about 17,800 students. About 81% of the students who graduate find a job in their field within six months. The school offers a range of programs—from a two-year associate degree to year-long technical training to certificate courses that might focus on a specific skill that can be completed in a matter of weeks.
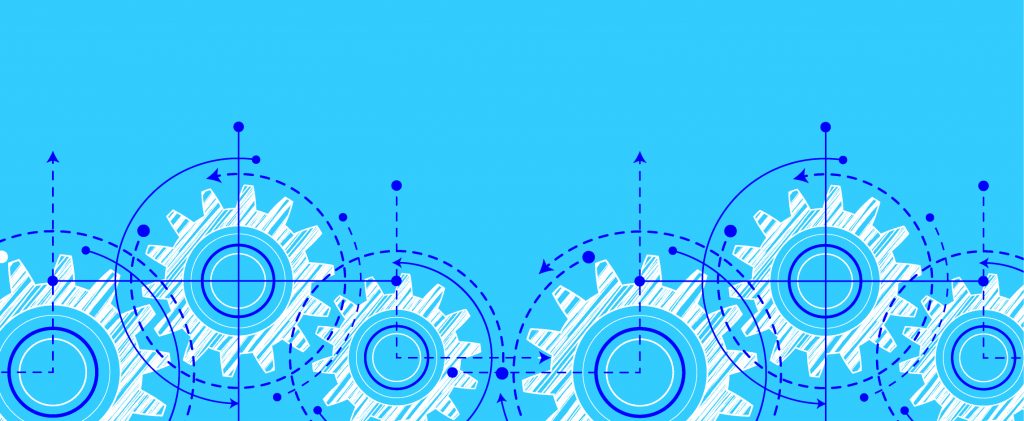
Graduates get good jobs, a point Barnhouse says must be made to parents. Parents often think the best path for their children includes a degree from a four-year college. However, trained WCTC graduates can land positions earning $50,000 to $70,000 per year—with benefits—depending on the trade, Barnhouse says.
“We need to change the perception of technical education and the trades to make it reflect what the reality is. It is not dark, dirty, and dusty,” he says. “It’s highly technical. It is extremely math-focused and it is safe.”
Because of the worker shortages, companies are increasingly moving toward automation. While those trends might reduce the need for people, the workers who remain must be highly trained to operate or maintain the machines.
“These are very skilled folks coming out,” Barnhouse says. He thinks workers are in a “golden age” where they can choose a career path from the start or shift to something new mid-career. Anecdotally, he says, a CEO of a metal fabrication company told him in June that he would hire 35 workers right away if he could find them.
“This worker shortage is going to get worse over the next five or six years and not get better,” he says. “The time is now to think about how you are going to do things locally.”
That might mean working with competitors to figure it out, he says. He also encourages companies to contact their local chamber of commerce and technical schools to brainstorm. Meanwhile, WCTC wants to coordinate with high schools so students can work simultaneously to get diplomas and an associate degree. Barnhouse learned that idea while serving at a Florida community college before taking the job in Wisconsin early this year. Students can get out of school with an associate degree—without debt—and start work immediately.
“The sooner we get people trained and educated, the better,” he says.
Building Courses
One person who works with companies to create WCTC courses is Michael Shiels, dean of the school of applied technologies. He oversees all of the programs on engineering, graphics, manufacturing, construction trades, and transportation.
A list of WCTC courses involving the printing industry includes one on color theory and print process, for example. Those are in addition to programs catered to the needs of companies.
“We have offered ‘boot camps’ for new pressroom employees in the flexo industry, which is an overview to the industry that gives participants basic skills and knowledge of terminology used to get off to a successful start,” Shiels says. “We also offered ‘orientation to print’ classes to provide new employees in different roles in printing companies general knowledge of the industry that also helps them get off to a successful start in the industry.”
Shiels, who has been teaching at technical schools since the mid-1990s, says demand for technical skills continues to increase as the number of people in the workforce declines. “People are still needed across all industries,” he says. “It has been difficult, and it continues to be difficult. Employers are going to need people who are more technically advanced than ever before.”
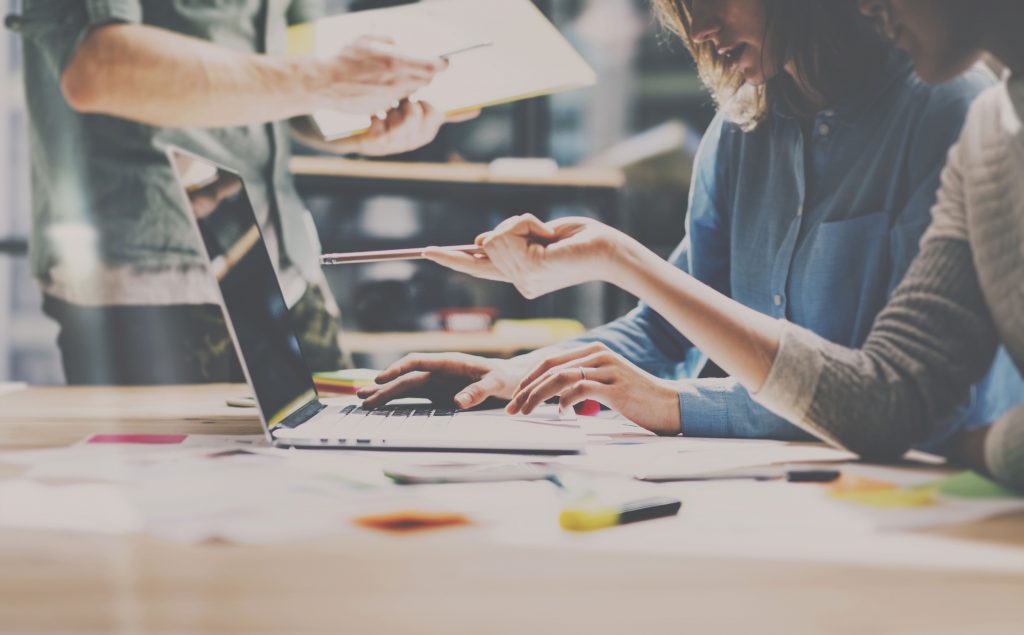
Reaching New Generations
Barnhouse’s advice to recruiting managers tasked with finding those workers is to study the new generation—Generation Z or people 25 and younger. These young people have a different viewpoint than people in earlier generations. Millennials, he says, were inclined to want to move from job to job.
“Not Gen Z,” Barnhouse says. “They would rather grow with a business and be engaged with an organization.” They are more interested in seeing the opportunities to learn with the same company through promotions rather than seek better pay by jumping around.
His other advice is for companies to demonstrate a clear interest in the environment if they want to attract younger workers.
“Every single company has to articulate on the front end how in some way, shape, or form that they are, in fact, in the business of environmentalism,” he says.
He gave an example of an industrial cleaning company that “cleans the stuff that others don’t want to clean.” The work is important, but the company needed to show how it reused water several times and that it kept dirty materials from entering the environment. “It’s an environmental company, not just a cleaning company,” Barnhouse says. “That will get the attention of Generation Z.”
For the flexible packaging industry that is dedicated to a circular economy and sustainability, with specific plans to achieve various goals, that thinking is something to tout.
“I would lead with that,” Barnhouse says. “That is one of the first things that is going to get the attention of someone 25 or younger. They can go to a company that already is concerned about the environment.”
Some of those dynamics were playing out in the programs the ELC recruitment committee created this summer.
Getting Started
During a summer networking program for interns set up by Shah’s committee, students were told about the opportunities but also the challenges in the flexible packaging industry, such as with recycling. Some of them say they didn’t know about the circularity efforts in the industry before their exposure to FPA.
The various forums held during the summer program, including one dedicated solely to sustainability, reinforced how the moves toward a circular economy have been one of the greatest challenges for the industry but also offer some of the most interesting career paths.
“As far as what interests me, I would say that it is the versatility of flexible packaging,” says Jackson Leffler, a senior at Michigan State University. He is studying packaging science with a minor in sustainability. “The opportunity is there in almost every market for flexible packaging to be a solution as far as cost savings or sustainability.”
Thomas A. Barstow is senior editor at FlexPack VOICE®.