As 2024 began to wind down, FlexPack VOICE® asked three experts involved with the Flexible Packaging Association (FPA) about key flexible packaging industry developments this year, while looking toward 2025 and beyond: Amanda Ciccone, senior director of sales at Dow; Dhuanne Dodrill, CEO of PAXXUS, Inc.; and Alison Keane, former president and CEO at FPA.
PAXXUS and Dow were asked to participate because they have the distinction of being among the longest-serving member companies of FPA. Dow has been a member for 55 years and PAXXUS for 30 years. Each year, FlexPack VOICE® recognizes companies that achieved five-year milestones with FPA; an article that reaches out to other FPA members begins on page 18.
Ciccone is a board member of FPA. And Dodrill, a past member of FPA’s board of directors, also serves as chair of the Sterilization Packaging Manufacturers Council (SPMC®), an FPA committee that engages with organizations focused on healthcare packaging.
Anticipating Change
Like companies in every industry, businesses involved with flexible packaging and its supply chain must keep an eye on macroeconomic trends, especially with indications that slower growth is expected in 2025.
“Continued uncertainty around the economy is leading customers to look for control, and ideally, reduce costs,” Dodrill says.
How much they are spending on packaging is a focus of those customers.
“As a result, our main challenges will be to continuously improve our operations to offset rising costs of labor and to effectively manage raw material costs to maintain a stable price for our customers,” she adds.
At PAXXUS, the disruptions caused by the COVID-19 pandemic led to rethinking supply lines, too, she says.
“A common theme we are hearing from our customers is the desire for localization,” Dodrill says about the aftermath of the pandemic. “Customers and the industry as a whole have become increasingly aware of how quickly the supply chain can change and now are seeking the added security of having suppliers more strategically located.”
This year, Dow continued to focus on the materials ecosystem around waste and all of the players across the value chain that work to build a circular economy for waste, Ciccone says.
“By ensuring all the technologies, processes, and design work together—from creating the initial design to be more recyclable to improving the systems that collect, sort, process, and deliver packaging—our focus was collaborating with innovative companies to keep material in the circular economy,” she says.
Increasing the circularity of plastics will continue to be a focus next year.
“Doing so offers key opportunities to minimize waste and to prevent leakage into the environment where waste is mismanaged while continuing to preserve the essential benefits offered by plastics, including food safety and offering innovations in construction, medicine, and transportation,” she says.
Regulations
PAXXUS officials know that staying ahead of industry trends and regulatory changes is essential, Dodrill says.
And regulatory challenges are a constant concern, says Keane, who left FPA at the beginning of August. Before her departure, she says, FPA had fulfilled its legislative goals in 2024. Minnesota was the only state to pass a new extended producer responsibility (EPR) for packaging bill this year. FPA supported the measure after working with the sponsor to change some of the provisions to be in line with FPA’s EPR for packaging policy.
“In addition, we were able to defeat several bad EPR for packaging bills such as one in New York,” Keane adds.
As FPA officials prepare for 2025, they expect EPR to remain a major issue, especially as Maine, Oregon, California, Colorado, and Minnesota move to implement their laws.
“The regulations putting these programs in place in each state are an enormous amount of work for both the state agencies writing them but also the industry’s response,” Keane says. “Each state’s legislation and regulatory process is different, and the details for compliance, and ultimately, the success of the program will come down to how the regulations are drafted.”
Monitoring those efforts will require industry focus for years, she says. Another focus will be on regulations of various chemicals such as per- and polyfluoroalkyl substances (PFAS), polyvinyl chloride (PVC), polyvinylidene chloride (PVDC), and bisphenol A (BPA).
In 2024, FPA worked to amend the Rhode Island PFAS processing aid ban law to give companies more time to comply while removing the ban on PVC and PVDC films contained in the same bill. A California bill banning PVC and PVDC films was defeated, Keane says.
“Chemicals of concern will continue to be a major issue for the industry, as we have seen it shift from banning individual chemicals such as BPA to whole classes of chemicals such as PFAS,” she says.
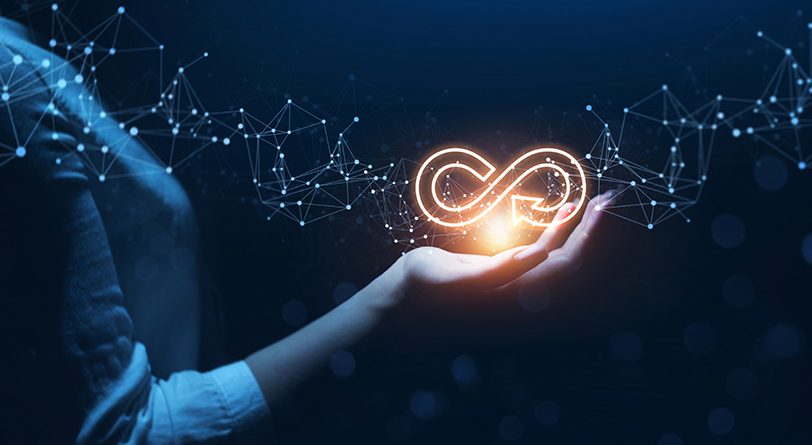
Regulators have moved to wholesale bans without doing risk analysis, and in many cases, there is no correlation to the chemicals themselves, Keane says. That includes proposed laws that would render a product or package nonrecyclable “merely because of the presence of the chemical and not based on actual recyclability or any health risk associated with that chemical contained therein.”
The situation with PFAS and similar regulations is a constant challenge for companies, including Ampacet Corporation, an FPA member celebrating a 15-year milestone in 2024. Ampacet does not produce flexible packaging but supplies the additives, colors, and white and black masterbatches used in packaging, says Brian Kannel, U.S. sales manager at the company.
Customers have been asking for process aids free of the chemicals. It also has been a challenge to develop additive technology for increased post-consumer resin levels and for maintaining physical properties and performance.
“These have seen the biggest interest from our customers in 2023–2024,” Kannel says. Innovation is critical to meeting the challenges, with the company launching masterbatch solutions free of PFAS.
Chemical and Advanced Recycling
The year 2024 saw some progress in getting chemical recycling technologies recognized and accepted as legitimate recycling forms in some states, Keane says. That is important because policymakers must first recognize chemical recycling technologies as legitimate recycling before the technologies can flourish.
“Without such, we will never have packaging for food, health, and medical products achieve full circularity,” she says. Without advanced recycling, it would be almost impossible to get some post-consumer packages back into packaging or other products, she cautions.
Keane also says EPR laws must use the fees collected through the programs to invest in advanced recycling infrastructure.
“These technologies have been around for many years and used in other sectors of industry,” she adds. “We now need to focus them on packaging, where needed. These technologies can and should be used in conjunction with mechanical recycling, but collection and sortation for streams that need chemical recycling need to be built in.”
Otherwise, if EPR programs only invest in current mechanical recycling systems, a substantial portion of packaging will be stranded.
“Flexible packaging, for example, has close to 60% of the market for food and beverage, so over half of what you see in the grocery store today is in or contains flexible packaging, and most of that isn’t getting recycled because the current U.S. recycling system doesn’t support it,” Keane says. “The U.S. needs to modernize its recycling programs. Over the next several years, we will see whether the EPR laws on the books will be successful in meeting that goal or whether they are just a way to pay for the status quo.”
One step backward happened in Maine, where a new law would prohibit the use of these technologies for recycling credits, she says.
Progress is being made, Ciccone says. In the U.S., companies have announced $17.5 billion in projects for advanced recycling, mechanical recycling, and recovery, she says, citing numbers from the American Chemistry Council.
“These commitments were made without regulatory certainty—but imagine what’s possible with clarity on regulations,” she adds.
Besides EPR, other policy considerations such as transparency in labeling, recycled content, and other specific targets will likely come into focus next year, Ciccone says.
“Given the ongoing Global Agreement on Plastic Pollution negotiations and upcoming INC-5 in November 2024, we are hopeful that a thoughtful final agreement—considerate of implementation realities and inclusive of all stakeholders—will be negotiated and settled,” she says.
“If we design products with their end of life in mind, we can create more products designed to help enable recycling, then, in turn, use the circular content in feedstock to produce plastics, helping enable brands to achieve their sustainable packaging targets.”
Amanda Ciccone, senior director of sales at Dow
Joint Efforts
Stakeholders often point to how governments must ensure a smoother transition toward sustainability, partly because of the need to harmonize policies nationwide but also because of the excessive cost of infrastructure.
“The government has a crucial role to play in developing a circular economy, but ultimately, it needs to be a collaboration between industry and government, especially regarding advanced recycling for flexible packaging,” Dodrill says. “The investment in necessary infrastructure is substantial, and without guidance and support from both industry leaders and federal officials, achieving effective adoption of the needed architecture will be challenging.”
She encourages the government to take an active role with organizations like FPA and the Healthcare Plastics Recycling Council (HPRC) to create a framework that encourages innovation and aligns with regulations.
“This approach can provide a lower barrier to entry, allowing for broader adoption of the materials created and offering a better value proposition for flexible materials as feedstock,” Dodrill says. “This collaboration can also help align efforts across different sectors, ensuring the move toward a circular economy is cohesive and effective. Ultimately, without support from government and industry, the transition to a circular economy may face significant hurdles and delays.”
In addition to SPMC®, PAXXUS is active with HPRC and Kilmer Innovations in Packaging, which fosters innovation in medical device packaging.
The goal is to create solutions for handling waste while ensuring patient safety is not compromised.
“Long-term, advanced recycling is a necessity, and we are part of HPRC’s work to demonstrate that this is a viable and economical approach for healthcare waste,” Dodrill says.
Sustainability Efforts
Many companies made pledges through organizations, including the Ellen McArthur Foundation, to have all their packaging recyclable or compostable by 2025, Keane points out. While some packaging has already achieved this, others such as flexible packaging have not.
“Most companies have already rolled back their commitments, and more will continue to do so to more realistic time frames, such as 2030, which mirror most of the EPR laws on the books,” Keane says.
Companies also are qualifying their commitments based on recyclability or compostability and not on whether the package is getting recycled or composted.
“While technically all packaging is recyclable today, regardless of the substrate (because the technologies to do so exist), the collection, sortation, and processing infrastructure does not exist. And often, the lack of end markets for the recycled product is not viable or simply not cost-effective,” Keane says. “Similarly, industrial composting infrastructure exists, but it is not readily accessible to most consumers in the U.S., and most often the programs do not want or take the packaging with the protein.”
That is where EPR systems for packaging that subsidize infrastructure investments are needed to scale up programs to create viable end markets.
For its part in addressing sustainability goals, PAXXUS focuses on reduction and recycling.
“For reduction, we are concentrating on minimizing the number of layers, passes, and overall thickness of our materials,” Dodrill says. “This approach not only reduces raw material usage but also lowers our environmental footprint by cutting down on the resources needed for production and transportation.”
On the recycling front, the company developed a line of single-polymer, recycle-ready materials specifically designated for individual recycling streams, she adds.
“These efforts are part of our broader commitment to sustainability and our drive to create packaging solutions that are both effective and environmentally responsible,” Dodrill says. “By continuously improving our practices, we hope to contribute positively to the environment while meeting the needs of our customers.”
Ciccone says Dow looks at the process with the end in mind.
“If we design products with their end of life in mind, we can create more products designed to help enable recycling, then, in turn, use the circular content in feedstock to produce plastics, helping enable brands to achieve their sustainable packaging targets,” she says. (More from the interview with Ciccone can be found at flexpackvoice.com.)
Thomas A. Barstow is senior editor of FlexPack VOICE®.