Companies across the supply chain in the flexible packaging industry have been working toward a circular economy for years. With recycling efforts and laws accelerating, and with consumer trends shifting, the Flexible Packaging Association commissioned a report to guide its more than 150 members with various roadmaps and proposals to facilitate the numerous goals.
The more than 200-page report—about half of which includes the appendix highlighting the research behind it—was released in December, with the authors giving a preview during the FPA 2020 Virtual Fall Executive Conference.
“As much as we try to predict out what 2030 will be like, we really are taking it from a perspective of this point in time of 2020,” says Todd Bukowski, who co-authored the study as a principal with PTIS, LLC. “We know technologies will change. We know there will be new types of legislation. There will be new collaborations. All of these will have an impact.”
Those dynamics make the report a “living document” that can be updated and refreshed as new initiatives and policies develop, Bukowski says. The study—A Flexible Packaging Path to a Circular Economy—was developed by PTIS and Priority Metrics Group, a business-to-business market research and analysis company. The report relied upon extensive interviews with more than 50 stakeholders, including people in the packaging value chain and associations, as well as brand owners, retailers, raw-materials suppliers, and consultants. The study also used primary and secondary research, which included global reports and initiatives, and a survey of FPA members.
Curt Begle, the 2019-2020 FPA chair, says that the report achieves the primary purpose of showing company leaders how to steer toward 2030.
“This can guide members, all of our members and other interested parties, on approaches into the future for flexibles,” says Begle, Berry Global’s president of health, hygiene, and specialties businesses. “… Obviously, this continues to be a topic for every one of us, and it’s a big topic for our customers.”
Many efforts are underway for a true circular economy that includes keeping plastics out of the environment. “We have to be part of the solution,” Begle says.
“The industry is starting to coalesce around this idea of a circular economy and getting materials back. It is a great time to be involved.”
—Todd Bukowski, who co-authored the study as a principal with PTIS, LLC
Kathy Bolhous, CEO of Charter Next Generation and the incoming 2021-22 chair of FPA, says that the industry proved its importance for health and safety during the pandemic. One goal will be to ensure that consumers remain aware of the benefits of flexible packaging, including the environmental benefits, moving forward.
“Flexibles are the optimum environmental choice because they reduce waste at every stage of its life,” Bolhous said during the Global Pouch Forum held this fall. “They require less energy to manufacture, generate less greenhouse gas emissions, use less water, and reduce transportation costs.”
The report outlines five “roadmaps” to help the industry drive toward 2025, 2030, and beyond, and Bukowski points out that the industry has the most control over the first part—design. The industry can take steps toward improving products toward circular economy goals, such as having a portfolio that is largely mono-materials by 2030, even though the availability of mono-material structures with barriers and high operational performance is limited today. The industry also could take other steps such as developing digital watermarks and chemical markers that will assist with the sorting of flexible packages. “Converters really only have control over the design phase,” Bukowski says.
The other roadmaps—detailing operations like collection, sortation, reprocessing, and end markets—have heavy interest from numerous stakeholders, from governments to foundations to consumers to brand owners and other industries. The flexible packaging industry needs to continue to have an interest, as well, so it ensures that the solutions, particularly recovery and recycling infrastructure, provide packaging with an onramp to circularity. So far, a fully coordinated effort with recycling infrastructure hasn’t been developed. “We don’t have a really strong recovery and collection and sortation system in place,” he notes.
The study recommends creating a Producer Responsibility Organization—or PRO—that can monitor progress and ensure that the funding and infrastructure have the best results for the industry. “We need to have really good collaboration with those leading with collection and sortation,” Bukowski says.
Stakeholders agree that moving toward a circular economy will be expensive and require massive investment, as well as various legislation.
“We know it is going to take an awful lot of funding. But, with that said, we know we are not alone on this journey,” he says.
One group that has been heavily involved is the Ellen MacArthur Foundation, which develops and promotes the idea of a circular economy by working with businesses, academics, policymakers, and institutions, according to its website. In 2016, the foundation set out to ensure three primary developments: that all plastics are made to circulate in the economy and out of the environment; that plastics that aren’t needed are eliminated; and that plastics that are needed are reusable, recyclable, or compostable.
The FPA study notes that the foundation created the New Plastics Economy initiative in 2018 that “applies the principles of the circular economy and brings together key stakeholders to rethink and redesign the future of plastics.” The initiative has more than 450 signatories and includes companies representing 20% of all plastic packaging produced globally, the report points out. All the consumer packaged goods companies (CPGs) that have signed on are fully committed to having their plastic packaging compostable, recyclable, or reusable by 2025.
“There is a huge opportunity to shift from single-use to reusable formats,” says Joss Bleriot, the Ellen MacArthur Foundation’s executive lead for institutions, governments, and cities when speaking about the plastics that are needed. “That requires a fundamental rethink of what is the product you want to deliver—rethinking, and redesigning of the packaging, sometimes even the product itself.” (Read our interview with Bleriot on page 8.)
Building Connections
Because of the push by brand owners to meet their goals, Bukowski says, the industry needs to stay connected to the various efforts. The report points out that the initial investment in collecting, sorting, and reprocessing will likely be geared toward rigid packaging, but much of that investment can apply to flexible packaging, too. Many traditional municipal recovery facilities were designed without flexible packaging in mind. However, the report also notes that a pilot program in Pennsylvania met most goals for flexible packaging to be collected, sorted, and made into products for various end markets.
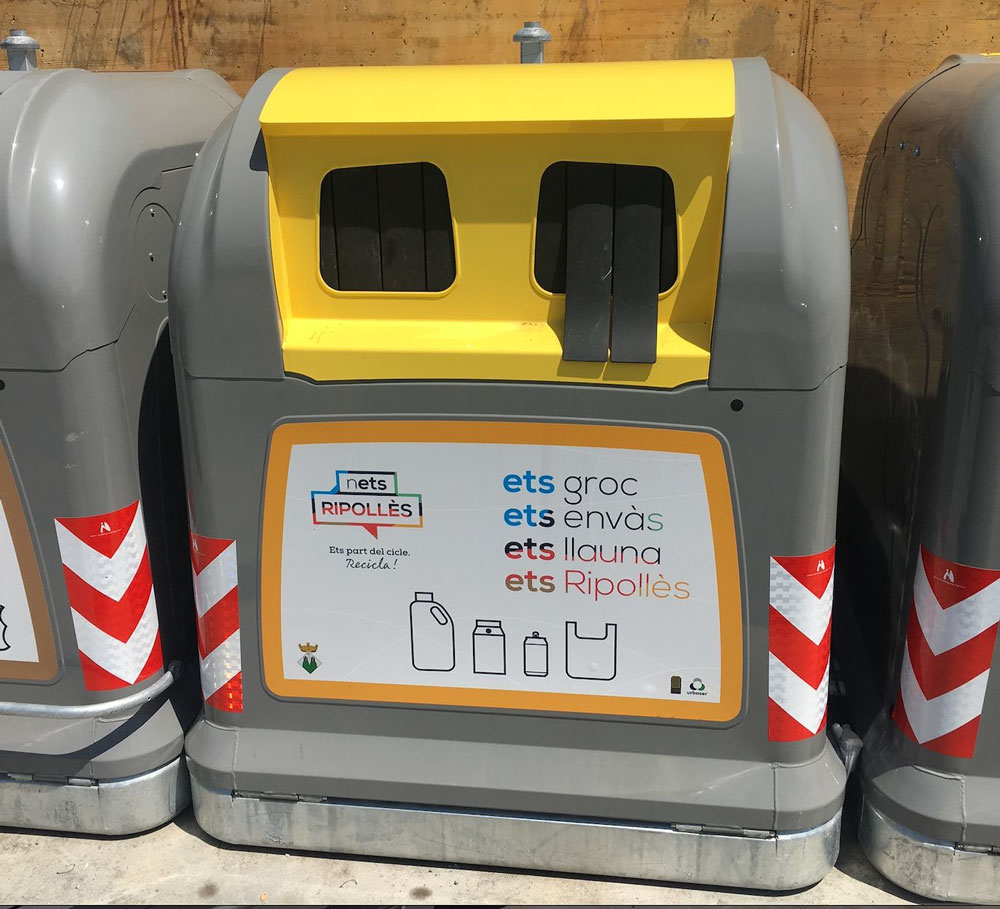
“It is critical for the industry to collaborate with others and ensure that the sustainability benefits already achieved through flexible packaging are further enhanced as it strives to embed itself into a circular economy framework,” the report reads. “In order to meet future state goals, it is critical that flexible packaging converters, as well as other value chains, initiate actions now to meet mid- and long-term objectives and circular economy goals.”
Lessons From Elsewhere
The industry can learn a lot from what other countries or cities are doing, whether it is the intricate collection and sorting systems in Barcelona, Spain, or efforts in British Columbia, Canada, where the flexible packaging recycling rate is 20%, Bukowski says. In the United States, the flexible packaging recycling rate is 4%, partly because consumers are confused by the myriad of systems in place—as well as the number of flexible packaging structures—plus the extra step of needing to take recyclable PE-based structures to retail stores (for drop off) instead of placing them in their curbside cart. The report, however, suggests that the U.S. recycling rate could be 30% by 2030.
The report primarily focuses on North America, while acknowledging that low flexible packaging recycling rates are a global issue. Guido Aufdemkamp, executive director of Flexible Packaging Europe, said during a presentation at the fall FPA forum that Europe is farther ahead in many ways. The United States can learn from some of the efforts in Germany, the Netherlands, and France, as well as Poland, where the investment in infrastructure is showcasing modern technologies that move a lot of volume with fewer workers.
In Europe, Extended Producer Responsibility fees are common, he adds. And starting Jan. 1, 2021, member states of the European Union will start paying .80 euros per kilogram of nonrecycled plastic packaging, with member states likely adding .20 euros for administrative costs.
Aufdemkamp suggests that the United States might be able to avoid extreme fees or requirements by working now to address circular economy issues. “I am confident that Americans, of course, because of their nature with freedom and they don’t like too much legislation, will not go this drastic route,” he says. “However, I am confident that you can manage it because you can pick the best practices from Europe and apply those.”
Finding Innovations
Each company can do its part by looking at what is being done for a circular economy and then ramping up those individual efforts, Bukowski says. He suggests that companies work with individual brands and then expand ideas—such as using digital markers for sorting—across their portfolios.
Improvements in advanced recycling—or processes that convert plastics in ways that plastics can be reused—continue to improve, as well. “Continued focus on innovation and technology development, such as advanced recycling, etc., is an essential part of roadmap development and implementation for flexible formats,” the report says. While pilot programs are working, the industry needs public support and steady investment to make advanced recycling widespread, Bukowski says.
Meanwhile, other efforts, such as composting, are gaining traction.
“Composting and reuse are going to be important players in the next coming decade,” Bukowski says. “They are playing a small role, a niche role today. These will be parts that will take on a larger focus over time.”
Bukowski says a lot of action is already in motion, which is where the report will be useful for FPA members.
“We all have seen how important sustainability has become and the impact on business,” Bukowski says. “The industry is starting to coalesce around this idea of a circular economy and getting materials back. It is a great time to be involved.”
Thomas A. Barstow is senior editor of FlexPack VOICE™.
Identifying Challenges
A report commissioned by the FPA—A Flexible Packaging Path to a Circular Economy—offers guidance on where the industry could be by 2030. It identifies a number of challenges, including the following:
- Development of high-barrier mono-material (or polyolefin-based) structures
- Lack of consistent recovery systems/rules across the country
- Lack of collection infrastructure for flexible packaging
- Limited value of flexible packaging that is collected today due to a lack of end-market applications and demand
- Value of PCR compared to virgin material in price and performance
- Need for infrastructure funding to support collection, sortation, reprocessing, and end markets
- Lack of ownership by any one entity for the recovery infrastructure, resulting in a lack of overall action
- Consumer education on the value of flexible packaging along with recycling options
Roadmaps to Follow
A Flexible Packaging Path to a Circular Economy report identifies five roadmaps to help steer the industry toward objectives by 2025, 2030, and 2040.
- Design: “Design is the primary roadmap area where flexible packaging converters have direct control. Focus for 2030 is on recyclability, compostability (for certain food service and closed-venue applications), and developing structures and technology to aid in the sortation, such as the incorporation of digital watermarks. The initial focus is on polyethylene (PE)-based structures, but longer term will include polypropylene- (PP) and even paper-based substrates.”
- Collection: “Identification of new programs such as curbside pickup, bulk flexible packaging collection (ex. master bag holding other flexible packaging), and drop-off stations/depots in urban and rural areas to enhance the convenience and expand the collection of flexible packaging.”
- Sortation: “Infrastructure investment will be critical, including optical sorters, artificial intelligence, robotics, as well as digital/chemical markers on flexible packaging to aid in efficiency and reducing contamination.”
- Reprocessing: “Development of additional cleaning infrastructure, along with mechanical recycling capabilities. Efficiencies in reprocessing will be aided through better sortation. By 2030, there will be commercialized examples of mid-sized scaling of advanced recycling, which will allow better use of flexible packaging back into new flexible packaging through virgin quality monomers.”
- End Markets: “Post-Consumer Recycled (PCR) requirements will be driven by brand owner goals (and likely some level of legislation), which will enhance end markets for flexible packaging by 2030. In the meantime, the industry will need to identify new end-market applications (ex. construction film, non-food, industrial, etc.). Post-consumer recycled (PCR) focus will initially be driven by rigid applications before starting to reach higher levels for flexible plastic packaging (FPP) by 2030.”