Six states have adopted laws that focus on regulating the intentional use of per- and polyfluoroalkyl substances (PFAS) in food packaging. In response, some customers are demanding packaging free of PFAS. The regulations, however, do not equate to a total ban on the use of PFAS, and the industry needs to do more to educate on the differences between PFAS and the fluoropolymers we use as polymer processing aids (PPAs). Fluoropolymers have distinct physical and chemical properties, which differentiate them from PFAS traditionally used as grease-proof coatings in paper food packaging.
The Flexible Packaging Association (FPA) is working on a legislative fix for Rhode Island that mistakenly banned the use of these PPAs in food packaging along with PFAS in general. This law will go into effect in 2024. Meanwhile, other state regulations are being implemented, and consumer product companies are understandably concerned. Suppliers and converters, however, should also be concerned. Packaging producers should not make blanket “PFAS-free” certifications and should communicate the safety and value of PPAs.
Fluoropolymers are not perfluorooctanoic acid or perfluorooctane sulfonic acid or other long-chain perfluoroalkyl acids, nor can they transform into those substances in the environment. Fluoropolymer PPAs used in film manufacturing have a high molecular weight, have very long-chain lengths (thousands of carbons long), are unreactive, and don’t break down into anything harmful or water-soluble. As a result, they are not found in sources of drinking water. Fluoropolymers are large, stable, inert polymeric molecules that are too large to cross biological membranes and, therefore, present little potential for human or environmental exposure.
In addition, fluorinated PPAs play a unique and highly beneficial role in the manufacture of polyolefin films used in food packaging. Impacts are reduced because improved material flow allows film thickness to be reduced thanks to more stable and smoother processes while also improving physical properties. Thinner films reduce virgin resin use as well as energy and water use in the manufacturing process, transportation impacts, and waste produced at end of life. Waste, energy, and environmental impacts are reduced as fluorinated PPA reduces downtime, increases run time, reduces scrap, and increases yield.
PPAs are necessary to incorporate recycled content into film, particularly at higher levels. Post-consumer and post-industrial resins can be incorporated into the new film, which cannot be achieved without fluorinated PPA. Not all resins melt and flow the same. As recycled content is incorporated, it may contain a blend of many different types of polymers, and PPA is needed to manage the flow without inclusions, haze, and other defects. Recyclers also use PPA, which makes the recycling of films easier and helps to retain the properties needed to enable the film to be incorporated again in downstream reuse and refabrication.
Alternative chemicals do not exist in the quantity and qualities necessary to replace fluorinated PPA for these applications, and until they do, FPA will continue to work to retain their manufacturer and use.
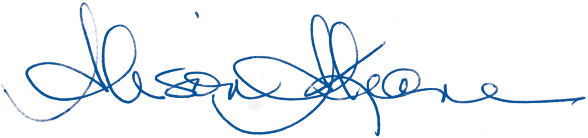
Flexible Packaging Association